本文已被:浏览 299次 下载 362次 |
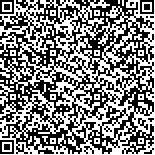 码上扫一扫! |
|
采用固有应变法预测超薄板的焊接变形 |
梁伟1,2, 周亮1,2, 孙晓露1,2, 邓德安1,2
|
1. 重庆交通大学 机电与车辆工程学院, 重庆 400074;2. 2. 重庆大学 材料科学与工程学院,重庆 400044
|
|
摘要: |
文中以汽车制造中常用的1 mm厚的薄板为分析对象,采用热-弹-塑性有限元分析了焊缝长度对固有变形分布特征的影响,通过比较热-弹-塑性有限元法及固有应变法预测的变形结果,定量分析了焊缝长度对固有应变法预测超薄板焊接变形时计算精度的影响.结果表明,当焊缝长度达到一定临界长度时,固有应变法可适用于板厚为1 mm左右超薄板焊接接头的焊接变形预测. |
关键词: 超薄板 焊缝长度 固有应变 焊接变形 有限元数值模拟 |
DOI: |
分类号: |
基金项目:国家自然科学基金资助项目(51375518);教育部留学回国人员科研启动基金;重庆市教委自然科学基金资助项目(KJ130401) |
|
Prediction of welding distortion in extra thin plate joint by means of inherent strain method |
LIANG Wei1,2, ZHOU Liang1,2, SUN Xiaolu1,2, DENG Dean1,2
|
1. College of Mechatronics & Vehicle Engineering, Chongqing Jiaotong University, Chongqing 400074, China;2. 2. College of Materials Science and Engineering, Chongqing University, Chongqing 400044, China
|
Abstract: |
Because the stiffness of extra thin-plate welded joint or structure is very small, welding distortion is apt to generate after welding. Therefore, it is very meaningful to predict welding-induced deformation accurately in such welded joint. Inherent strain method is a practical approach which can be used to predict welding deformation in large and complex structures. However, this method is seldom employed to estimate welding deformation in extra thin-plate joints. In this study, the features of inherent strain distribution in bead-on joint with 1 mm thickness was investigated by means of thermal elastic plastic finite element (T-E-P FE) models. Meanwhile, the influence of weld length on the distribution of inherent strain was also clarified. Moreover, the welding deformation in extra thin-plate joints with different weld lengths was calculated by using inherent strain method. The comparison between the results obtained by inherent strain method and those computed by T-E-P FE models shows that when the weld length is up to a critical value, the inherent strain method can be used to predict welding deformation in the extra thin-plate joints. |
Key words: extra thin plate length of weld inherent strain welding deformation finite element |